Print your own radiation shielding?
Chris Fox, Senior Medical Physicist, Peter MacCallum Cancer Centre, Australia
At some stage everyone who works with radionuclides and x-rays has wanted to shield some source. For a hundred years or so, the standard way of doing this has been to stack up lead bricks or hammer out a sheet of lead into some simple shape, but how nice would it be if we didn’t have to use lead. Lead is a toxic metal and wherever possible it is now being systematically removed from workplaces around the world.
Suitable replacements are not always easy to find: we need high density, high Z materials that are easily worked, non-toxic, not radioactive, and not too expensive Gold for example would be lovely to use, but there’s an obvious problem!
Tungsten is an interesting possibility. Amazingly dense, it can pack a lot of matter into a very small volume and is just about as dense as gold.
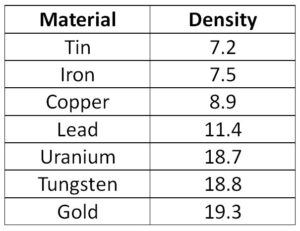
It would be great to be able to make shielding from tungsten, but there are a few problems with tungsten too. It’s a very hard material and machining it into shape requires very hard and sharp tools and lots of machine power, and there’s a lot of heat to dispose of in the machining.
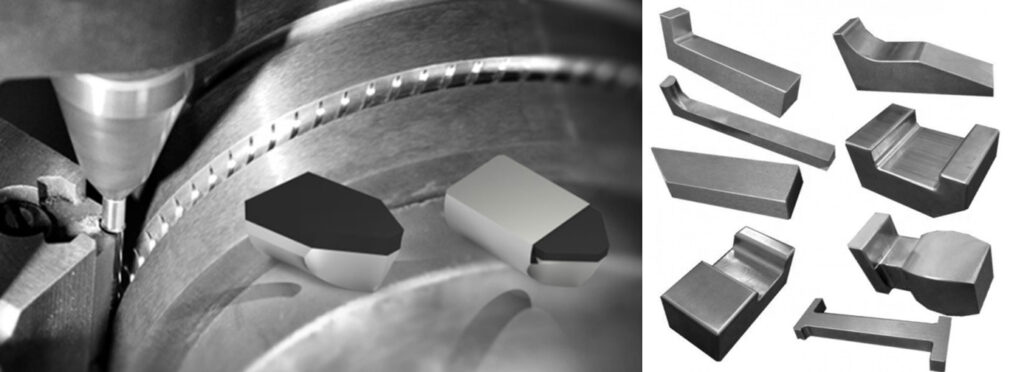
In the last couple of years however, a new option has emerged. Fine tungsten powder dispersed in a plastic can be melted and pushed out through a nozzle – which means it can be 3D printed. Currently commercially available materials have up to 17% by volume of tungsten powder in a matrix of PET-G (glycol-modified polyethylene terephthalate – best thought of as soft drink bottle plastic). The 17% by volume gives the plastic enough density to be useful for shielding against soft x-rays and electron beams.
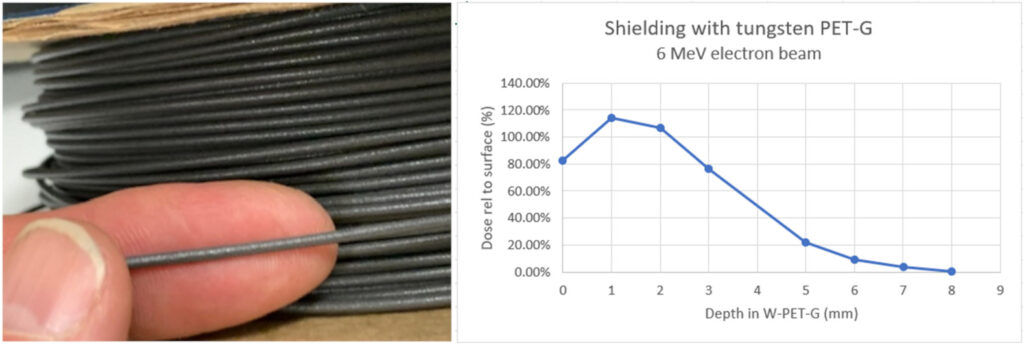
The shielding printed this way can be used to shape radiation treatment fields such as this surface shield for a leg treatment shown in figure 3.
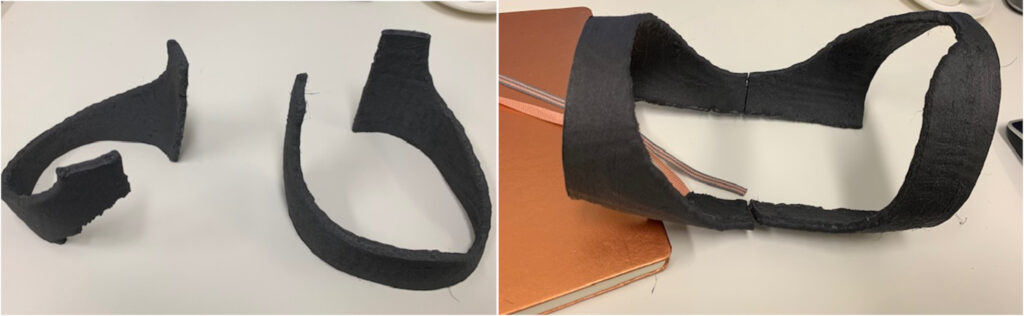
Work is going on at the moment to increase the fraction of tungsten powder in the filament. One manufacturer informs us that it may be possible to successfully print up to 50% metal powder by volume which would give the printed material a density comparable with lead. So the future is full of possibilities!